Tim Kelly from MEF (Manufacturing Excellence Forum) organised the eVTOL Student Team to visit One Composites this morning, with a tour from owner, Dave Biggar. Dave showed a full-scale autonomous drone concept for a military tender. He talked through some of their development process, which includes the use of the largest 3D printer in the southern-hemisphere. The printer doubles as a CNC machine, and they have a large robot arm that can do CNC work with finer precision.
Some takeaways:
- develop in the method that has the least friction. The easiest/simplest/fastest way to do something is best. My addition: this dovetails nicely with Elon Musk‘s 5-step philosophy of simplification and iterating until you have the simplest and best solution.
- have the 3D/CAD person as knowledgeable as possible in the process of manufacturing/finishing components. Ideally in direct communication with the manufacturing team, or is one of the team themselves.
- if there are multiple people involved, ensure the design engineer provides clear instructions to the people in the component creation and finishing team. Dave seems like a pretty chill guy, but says when this doesn’t happen, it’s one of the things that really frustrates him.
- when submitting a military tender, One Composites developed a full-sized, concept autonomous aircraft drone – in 20 days. They figure that showing their capability in rapid prototyping and development is a competitive advantage over submitting just a document.
- their $2 million large-format 3D printer has many limitations that a small-scale 3D printer does not have. One thing I’ve heard them mention multiple times, after visiting One Composites twice now (the first time was thanks to Tim in a group MEF visit), is that it can’t print downhill. Without seeing the printer in action (will happen at a later date), after seeing them slice our VTOL 3D model, it seems that the printer prints in a continuous fashion, and prints each layer at roughly 45º slices. The angle must be adjustable, as they mention that they prefer to either print a model vertically (in Dave’s words: “Mr Whippy” style, in a humorous reference to the Australian ice-cream van that dispenses ice cream in a cone in a continuous, circular method). Will be great to see how it works when we return.
I took a little footage from the morning:
Footage shot with GoPro Max 360º camera, and a GoPro HERO10 Bones on a small FPV drone.
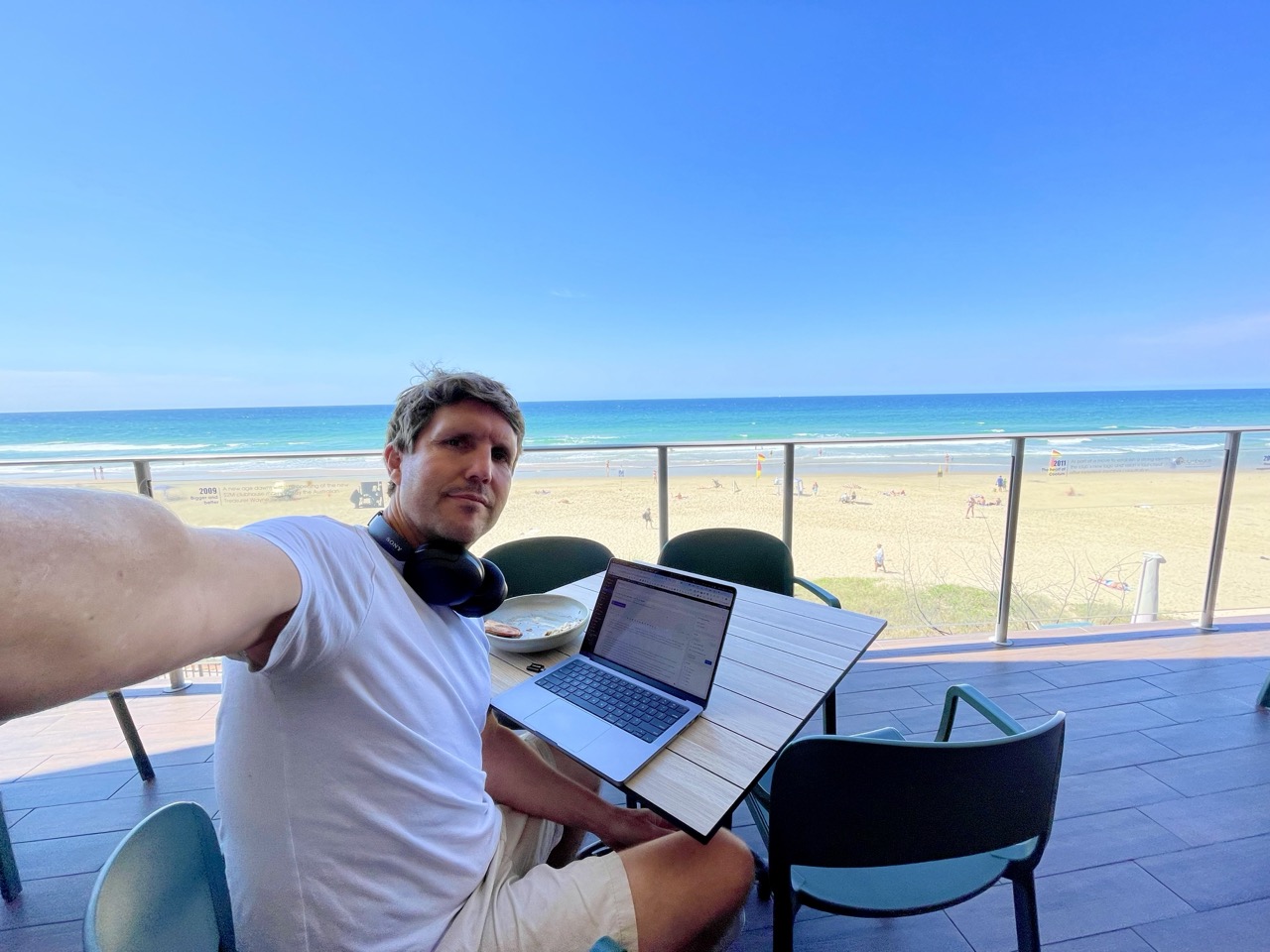
Wrote this first Notes on Life from Coolum Surf Life Saving club. No smile?! haha, I was very happy to be here, but behind me was a packed restaurant, so I think the smile felt a little show-offy (technical term 😆).